Kanban
Kanban ist eine Methode aus dem Lean Management, um den Materialfluss zu steuern. Karten steuern das Material. Kanban (jap. Kan = Signal, Ban = Karte).
Zielsetzung
- Reduzierung der Beständen
- Erhöhung der Lieferfähigkeit
- Verkürzung der Durchlaufzeit
- Bedarfsorientierte Produktion
- Reduzieren von Fehlern
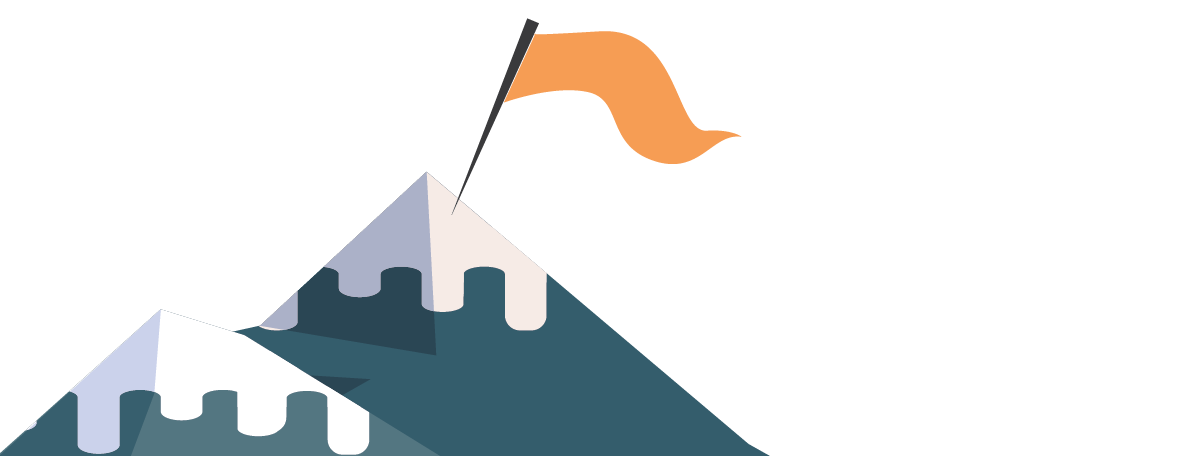
Vorgehensweise:
Jedes Teil wird einem Behälter zugeordnet mit einer definierten maximalen Füllmenge. Dieser Behälter wird vom Lieferanten bis zur Maschine eingesetzt.
Zu jedem Teil erzeugen Sie mindestens eine Kanban-Karte.
Informationen auf der Karte:
▪ Bezeichnung
▪ Anzahl der Teile (Füllmenge)
▪ Verbraucher und Lieferant
▪ Die Kanban-Karte ist eine Bestellkarte
Ist der Behälter leer so wird dieser zum Lieferanten geschickt. Im Normalfall existiert ein zweiter Behälter damit man weiterarbeiten kann. Der Lieferant füllt den ersten Behälter auf.
Das Steuerungsprinzip baut auf Regeln auf:
▪ Der Prozess wird immer vom Verbraucher ausgelöst
▪ Teile werden nur in Standardbehältern geliefert
▪ Es sollten nicht mehr aus den Behältern genommen werden als notwendig ist
▪ Die Kapazität muss vorhanden sein
Kanban-Karten müssen angepasst werden. D.h. die Informationen auf den Karten sind nicht in jedem Unternehmen gleich.
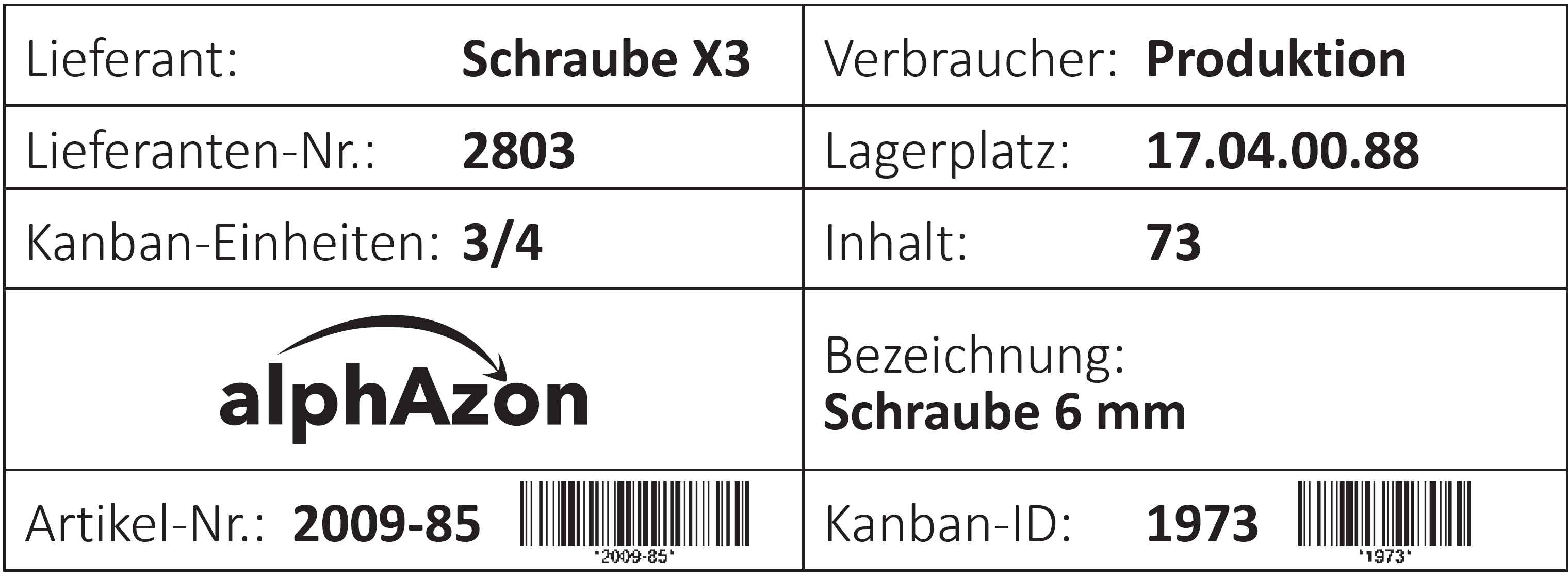
Das Kanban-Board visualisiert den Prozessablauf und zeigt an, wo sich der jeweilige Behälter befindet. Die Kanban Karten wandern von Spalte zu Spalte, bis die Aufgabe „fertig“ ist.
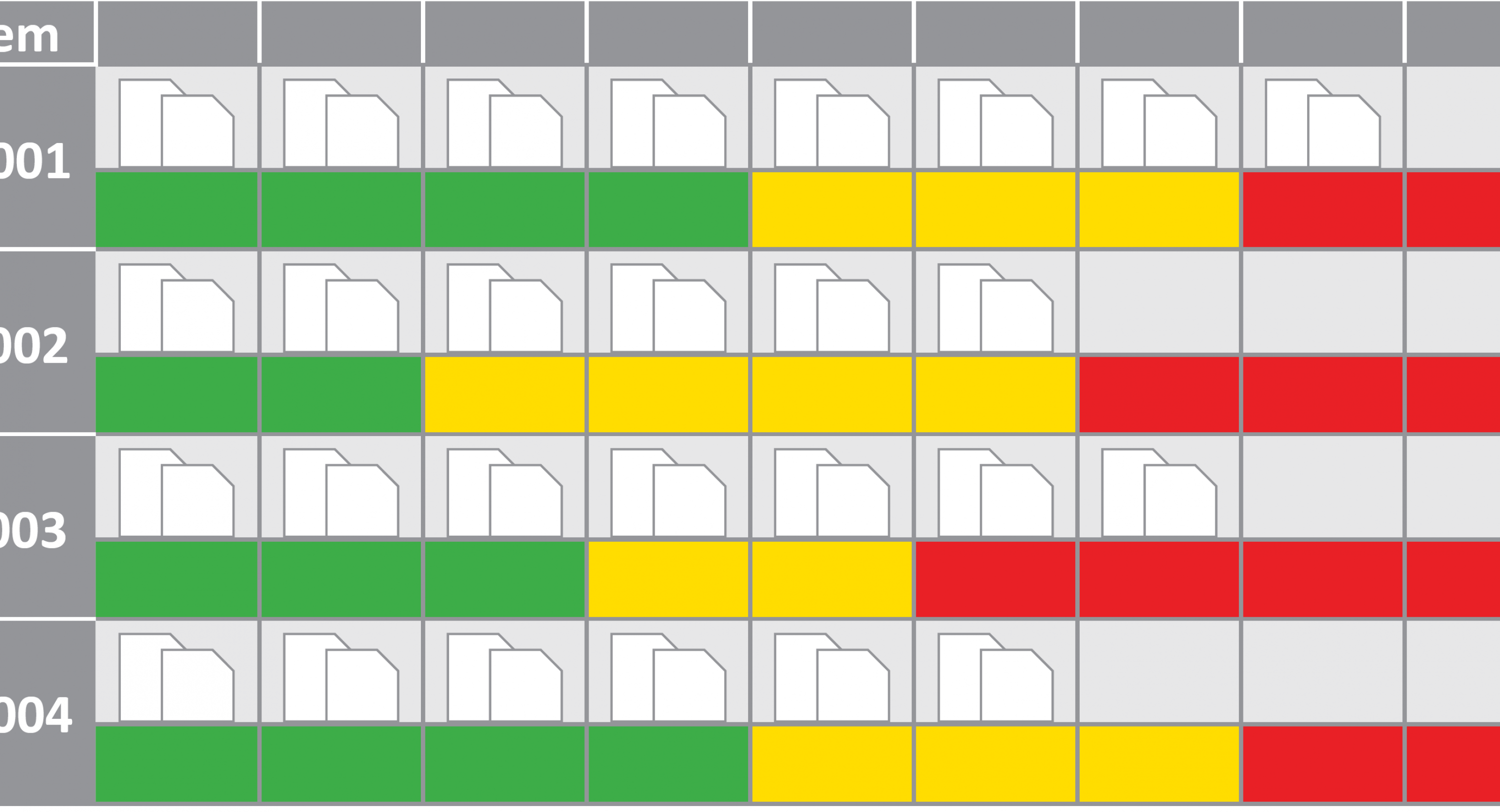
Gemäß dem Pull-Prinzip, wird nur das produziert, was vom Kunden benötigt wird. So können nicht weitere Bestände entstehen.
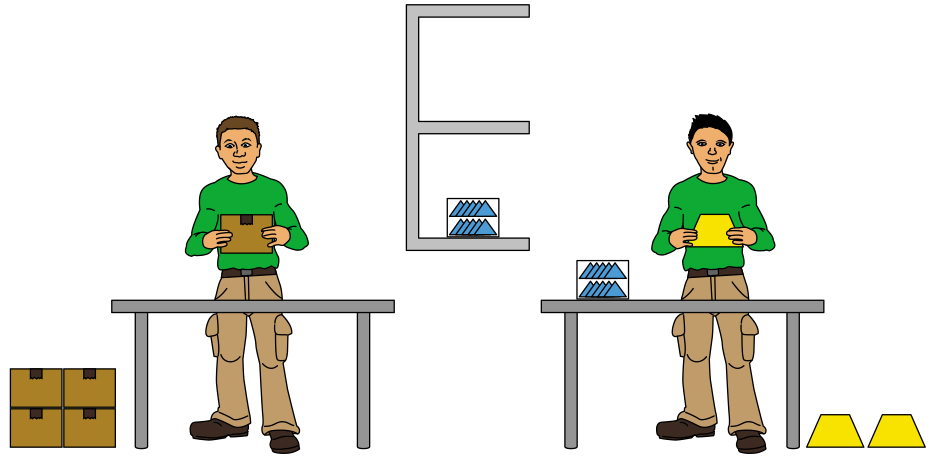
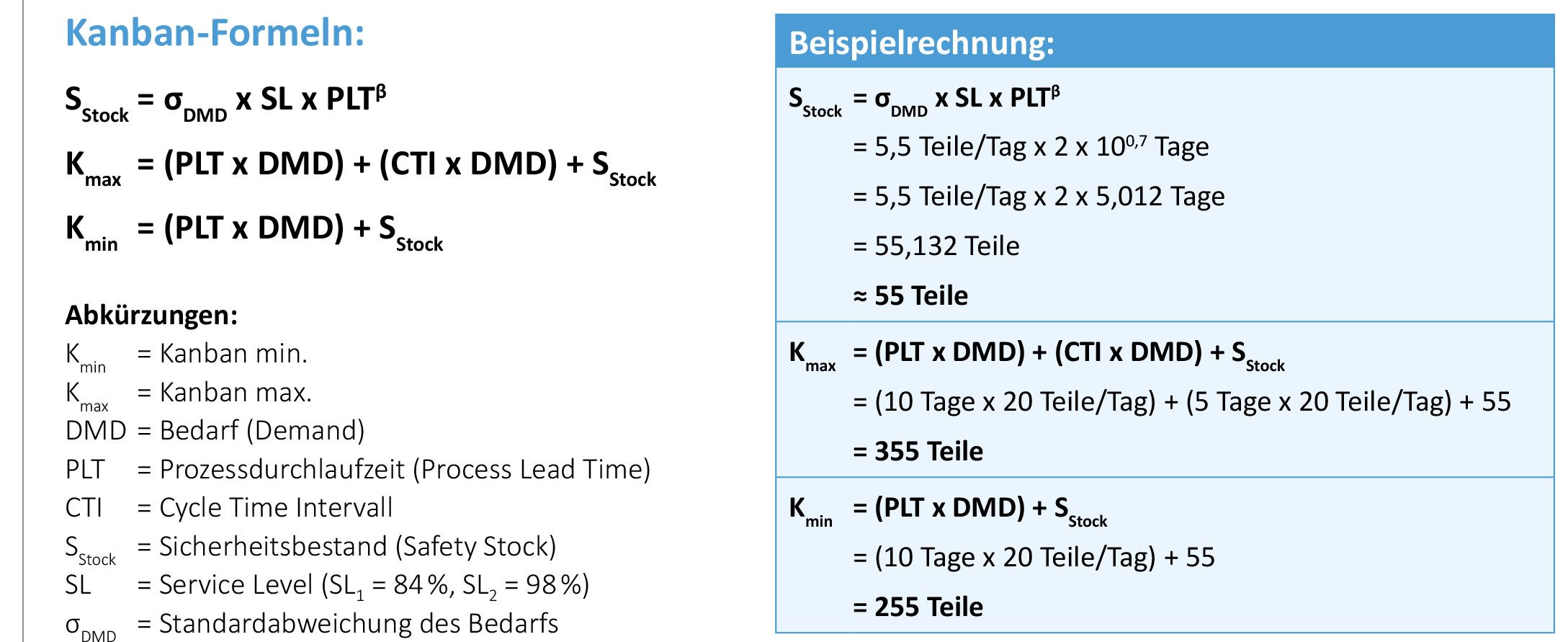