
Manufacturing GmbH
With great pleasure, we would like to congratulate
Zimmer Switzerland Manufacturing GmbH on being awarded the Shingo Bronze Prize 2024.
Zimmer is the first company in Switzerland and the second company in the entire German-speaking world to receive this prestigious award. We would like to congratulate Zimmer Switzerland Manufacturing GmbH on this exceptional achievement!
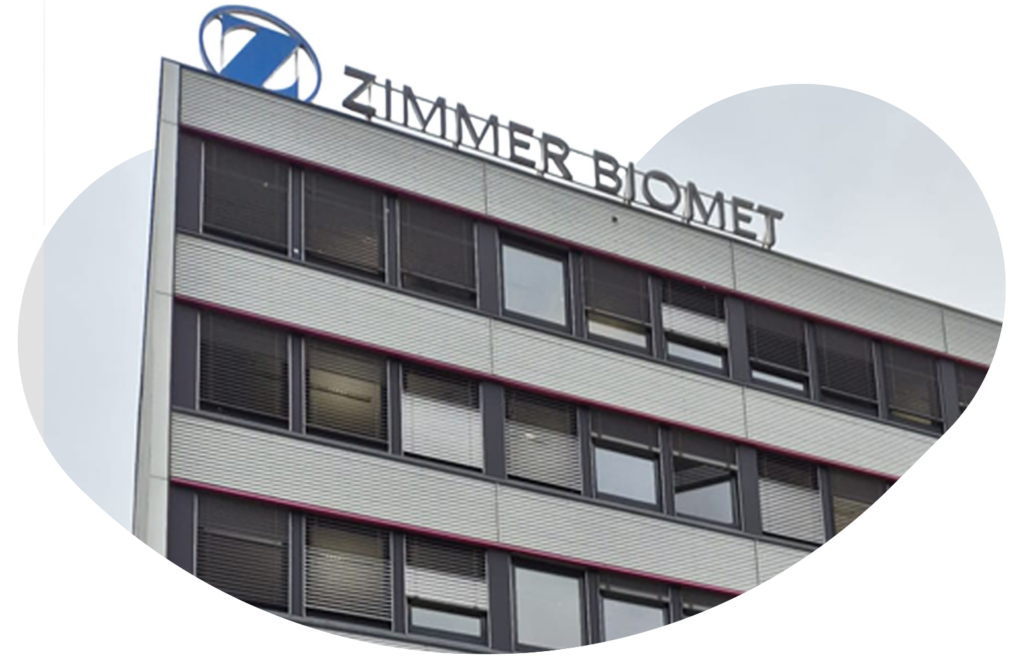
Home of the Shingo Prize
The Nobel Prize in Manufacturing
The Shingo Institute is the home of the Shingo Prize. The Shingo Prize, is an internationally renowned award, also known as the “Nobel Prize for Manufacturing” (Business Week), which recognizes companies that demonstrate a culture of continuous improvement (CIP).
The Shingo Institute is a department of the Jon M. Huntsman School of Business at Utah State University and is named after the Japanese industrial engineer and Toyota consultant Shigeo Shingo. Dr. Shingo distinguished himself as one of the world’s thought leaders in concepts, management systems and improvement techniques known as the Toyota Production System.





